
InShaPe
![[Translate to Englisch:] InShaPe](/fileadmin/user_upload/BayFOR-bilder/projekte/BayFOR-inshape-components-manufactured-by-powder-bed-fusion-li.jpg)
EU project InShaPe – next innovation leap in metal-based additive manufacturing
In many industrial sectors, such as the automotive industry, aerospace and the energy sector, the demand for lightweight, high-strength and mechanically highly resilient special metallic components is increasing. Modern gas turbines, for example, require extremely stable and at the same time lightweight heat shields. An important manufacturing process for this is the powder bed-based additive manufacturing of metals. This method is technically referred to as powder bed fusion of metals using laser beam (PBF-LB/M).
Depending on the application, the process is not yet always competitive compared with conventional production in terms of unit costs. The InShaPe research and innovation project, funded by the EU with EUR 6.8 million, aims to make a decisive contribution to the further development of the technology. Under the coordination of the Technical University of Munich (TUM), the Professorship for Laser-based Additive Manufacturing, ten partners from seven countries are working together on the project.
In powder bed-based additive manufacturing of metals, metal powder is applied to a building platform in an extremely thin layer of around 50-80 µm. This powder layer is melted by a focused laser beam and binds to the underlying material layer during solidification. This process is repeated layer by layer until a finished component is created. Complex and weight-saving geometries can be realised thanks to the layered structure. Excess powder is removed from the finished component, which is then usually reworked depending on the application.
Flexible adaptation of the laser spot enables efficient and cost-effective production
The aim of the recently launched InShaPe project is to further develop metal-based additive manufacturing. The improved manufacturing process is based on a high-performance optical module with programmable intensity distribution and AI techniques to determine the optimal beam shape for the target object, for example, determined by the material type and geometry. InShaPe is also developing an innovative process monitoring and control system for quality analysis that integrates the simultaneous observation of heat and process radiation of different wavelengths (multispectral imaging) into the area of additive manufacturing.
“The combination of these two new technologies enables efficient and advanced exposure strategies so that even the most demanding production of complex special components works right away,” says InShaPe coordinator Prof. Dr.-Ing. Katrin Wudy from the School of Engineering and Design at the Technical University of Munich.
InShaPe makes metal-based additive manufacturing faster, cheaper and more sustainable
The consortium has set itself the goal of further developing this form of additive manufacturing into a commercially wide-ranging manufacturing technology that will outperform conventional manufacturing processes such as die casting in terms of precision and sustainability in the future. The adaptation of the laser beam shape and the new exposure options enable an energy- and material-efficient production process. At the same time, InShaPe innovation in unit costs, flexibility and production volume is intended to demonstrate the competitiveness of additive manufacturing compared to traditional manufacturing processes. The AI-supported control and operation should also enable non-highly qualified workers to use the new procedure.
The overall goal of InShaPe is to further develop and demonstrate an innovative powder bed process for metals (PBF-LB/M) for four industrial applications in the aerospace, energy and automotive industries. Compared to the current state of the art, the following goals are to be achieved:
- a seven times higher production rate
- over 50 percent lower costs
- 60 percent less energy consumption
- 30 percent less waste
In the long term, the successful development and marketing of InShaPe technologies is intended to strengthen the European PBF-LB/M manufacturing industry as a leading provider of highly complex parts and set new best-in-class standards for digital, resource-conserving and agile laser-based production methods.
About the EU project InShaPe
InShaPe started on 1 June 2022 and will run until the end of May 2025. The project is being carried out by the Technical University of Munich with nine other partners from Germany, France, Israel, Italy, the Netherlands, Sweden and Spain. The project is managed by Prof. Dr Katrin Wudy, Head of the Professorship for Laser-based Additive Manufacturing at the Technical University of Munich. Other German partners include EOS, Oerlikon AM and the Bavarian Research Alliance. The EU is supporting the project with EUR 6.8 million under the European Framework Programme for Research and Innovation, “Horizon Europe”. Of this funding, EUR 3.8 million will be received by Bavarian stakeholders.
Project aims and fields of work
The overall goal of InShaPe is to develop and demonstrate an innovative powder bed process for metals using laser beam (PBF-LB/M) for four industrial applications in the aerospace, energy and automotive industries.
Compared to the current state of the art, the new process has the following advantages:
- a seven times higher production rate
- over 50 percent lower costs
- 60 percent less energy consumption
- 30 percent less waste
In the long term, the successful development and marketing of InShaPe technologies is intended to strengthen the European PBF-LB/M manufacturing industry as a leading provider of highly complex parts and set new best-in-class standards for digital, resource-conserving and agile laser-based production methods.
Target groups
- PBF-LB/M manufacturers, i.e. the users and players of PBF-LB/M technologies, which produce complex components according to customer specifications
- Technology providers/end users, i.e. the technology companies that rely on the services of PBF-LB/M manufacturers to produce complex components, e.g. in the automotive, aerospace and energy and medical sectors
- Scientists conducting research in the following fields: Technologies for production using photonic technologies; industrial sensor technology; application of data-controlled tools in production processes
- Machine tool OEMs and suppliers, i.e. manufacturers and distributors of PBF-LB/Mtechnologies for additive manufacturing (including supporting components such as sensors)
- Regulatory and standardisation bodies that regulate the application of PBF-LB/M procedures
- The general public, i.e. EU citizens interested in innovative, resource-efficient manufacturing and/or AI innovations, especially young people considering a scientific career
BayFOR as a partner
During the application phase, BayFOR supported the coordinator and the consortium in the technical and content-related conceptual design of the EU application as well as in clarifying financial and administrative issues. As a sponsored partner in InShaPe, BayFOR assumes the tasks of financial and administrative project management as well as communication with the public and interested expert groups.
Funding period
From 1 June 2022 to 30 May 2025, the EU Commission is funding the research project under the Horizon Europe funding programme with EUR 6.8 million, of which EUR 3.8 million for Bavaria in accordance with grant agreement no. 101058523.
Consortium
Under the coordination of the Technical University of Munich (TUM), nine other project partners from seven countries (Germany, France, Israel, Italy, the Netherlands, Sweden and Spain) are participating in InShaPe, including four from Bavaria:
Coordination: Technische Universität München, Deutschland
Project partner:
Aenium Engineering, Spanien
AMEXCI, Schweden
Bayerische Forschungsallianz GmbH, Deutschland
BEAMIT Group, Italien
Eindhoven University of Technology, Niederlande
EOS GmbH Electro Optical Systems, Deutschland
Oerlikon AM Europe GmbH, Deutschland
SILIOS Technologies, Frankreich
Technion – Israel Institute of Technology, Israel
Project coordinator: Prof. Dr.-Ing. Katrin Wudy, Technische Universität München
Contact
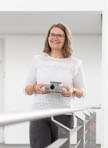
Prof. Dr. Katrin Wudy
Faculty of Mechanical Engineering
Technische Universität München
Phone: +49 (89) 289 - 55320
Email: katrin.wudy@tum.de
Contact at BayFOR
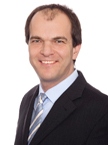
Dr. Nico Riemann
Deputy Head of Unit and Scientific Officer Information & Communication Technologies |
Engineering & Natural Sciences
Phone: +49 911 50715-910
Email: riemann@bayfor.org, harwin@bayfor.org
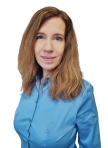
MBA Simone Wiegand
Project Manager ICT, Engineering & Natural Sciences
Phone: +49 89 9901888-134
Email: wiegand@no-spam-pleasebayfor.org